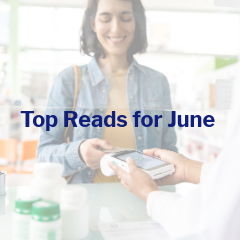
The top three Prescribed Perspectives articles downloaded by health systems in June.
Essential steps to help health systems better prepare for disruptions.
By
Date
February 07, 2022
By: Barry Cook
Read time: 1 minute
Since the early 1980s, the United States has seen a 50% increase in natural disasters like hurricanes, tornadoes and floods.1 During roughly the same time frame, mass shootings with three or more fatalities have surged from one or two per year to an average of one per month.2 Health systems can be better prepared to establish continuity of care in a disaster by developing a comprehensive emergency plan and cultivating strong relationships with distribution partners. Essential steps for successful planning include:
1. Make sure pharmacists have a seat at the planning table.
Pharmacists have the professional training and hands-on experience to recommend the types and volumes of supplies that particular disasters require — plus experience managing emergency storage and staffing issues.
2. Collaborate and communicate with drug distributors.
Open communication with drug distributors can help health systems prepare for the worst and adapt their disaster plans to reflect real-world, real-time supply chain challenges.
3. Map out emergency Rx orders ahead of time.
Pharmacy leaders should create templated disaster orders with essential medications and supplies and let their distributors know as soon as possible when a disaster order will be coming their way.
4. Include decision-makers on your crisis and recovery teams.
Health systems need people on the scene who are authorized to make decisions quickly and adapt as the situation evolves.
5. Plan for drills and drill the plans.
From verbal walk-throughs to full-scale disaster exercises, emergency drills help increase the staff’s comfort level while revealing any gaps to be addressed.
A trusted distribution partner can help health systems employ data from other emergency events to choose what drugs and supplies, in what quantities, to include in disaster orders. Distributors routinely help their partners navigate disasters and are a reliable source for real-world insights. They also take their own advice to disaster-proof the supply chain as much as possible.
Additionally, distributors maintain backup generators and fuel supplies. They keep staff and customers apprised of any special circumstances that could affect deliveries and work to overcome transportation challenges. They also share security resources or ship combined orders to facilitate disaster deliveries.
Experienced distributors maintain business continuity plans to ensure consistency during disasters. For example, McKesson’s program prioritizes protecting customers, ensuring the safety of their employees, keeping workplaces safe and secure, and ensuring the continuity of critical business processes following natural disasters, human-caused threats, public health emergencies and other incidents. We commit to safeguarding employees, mitigating negative impact to customers and ensuring clear and open communications throughout a disaster. We also focus on a return to critical services such as order management, fulfillment distribution, and service —as soon as possible.
1“Disaster & Mass Casualty Preparedness: Case Examples of Planning for the Anticipated and the Unthinkable. (ASHP presentation, June 26, 2019).” Kara L. Birrer, Heather Easterling and Kuldip Patel
2“US Mass Shootings, 1982-2021: Data From Mother Jones’ Investigation.” Mark Follman,Gavin Aronsen and Deanna Pan, Updated 5/26/2021. Accessed online 9/4/2021: https://www.motherjones.com/politics/2012/12/mass-shootings-mother-jones-full-data/