Read time: 5 minutes
Distributing one-third of prescription medications across North America is no small feat, especially when we complete 40,000-plus individual deliveries per day, and countless healthcare workers lean on our solutions to administer better care.
That’s why we’re constantly evolving our suite of distribution offerings to sustain our longstanding legacy of innovation in the pharmaceutical supply chain, which spans nearly two centuries.
Below, we highlight three solutions in particular that advanced the speed and accuracy of our pharmaceutical delivery capabilities so patients can access their medications with ease.
Innovating throughout history to move healthcare ahead
A faster way to order medications
The process of ordering and shipping medications from our distribution centers to places of care is a complex endeavor. In one day alone, we can fill 1.4 million line orders for our customers which contain medications and supplies.
With innovation at the core of everything we do, we found several ways to streamline this massive process over the years by leveraging cutting-edge technologies to save time and reduce paperwork.
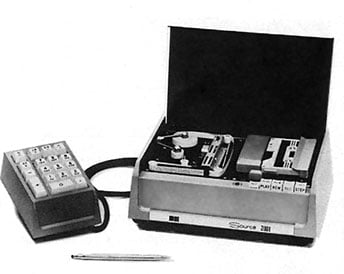
The EconomostTM by McKesson.
Enter The EconomostTM by McKesson. Launched in the 1970s, it was the market’s first electronic order transmission system that revolutionized pharmaceutical distribution.
While this type of solution might seem straightforward in today’s digital age, when it was first introduced, it dramatically improved the process for our customers who were used to submitting their orders by hand. The EconomostTM improved order accuracy by relaying orders through handheld pads and telephones.
Of course, as technology advanced, so did we. Using the basic principles of The EconomostTM, we modernized the solution and built McKesson ConnectSM.
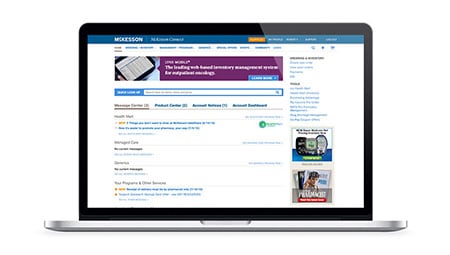
McKesson ConnectSM portal.
A first-to-market offering, McKesson ConnectSM is an online ordering system that helps customers submit and track orders, process returns, conduct inventory checks, and search our expansive product catalog for essential items they need to provide care. Now a mobile-friendly program, there are several interactive features, like a digital community, so pharmacists can chat with each other in the platform.
And McKesson ConnectSM continues to evolve since its marketplace debut in the 2000s. With nearly 3 million orders placed monthly in the platform, McKesson ConnectSM now includes advanced ordering software, which increases functionality and inventory management – and we continue to add new features based on our customers’ needs.
Tracking products and data with incredible speed
With hundreds of thousands of products and millions of stock-keeping units (SKUs) passing through our 30 distribution center doors on any given day, we lean on barcodes – and more recently Quick Response (QR) codes – to catalog and track large quantities of goods.
When barcodes first emerged in the 1980s, we saw an opportunity for this new technology to support the unique requirements of pharmaceutical distribution, especially due to the immense product variety, value, need for instant identification, and regulatory requirements of medications.
So, it inspired us to engineer a state-of-the-art solution: Acumax®, a warehouse management system (WMS) specifically designed for our distribution centers.
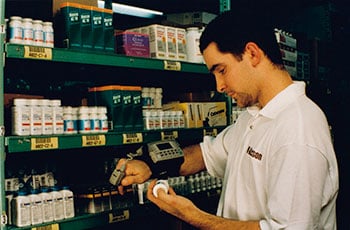
First-generation Acumax®.
The first-generation system launched in the early 1990s. And while Acumax® has advanced quite a bit since then, it remains one of our top distribution achievements to-date, even receiving industry recognition like the Computerworld Smithsonian Award for information technology innovation.
It’s still the only home-grown proprietary WMS in use in the market that’s built to support the healthcare industry to this day.
And we’re continuing to advance. Acumax® upgraded from reading barcode codes to scanning QR codes – which present data to any scanning device far more quickly.
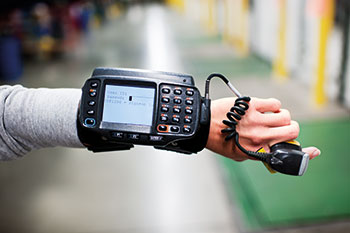
Acumax® today.
With QR codes’ immense information storage capacity, we’ve been able to eliminate the use of scanners, which are bulky for our workers to carry, in some of our distribution centers.
Acumax® is now a wireless system worn on the wrist and provides precise order accuracy to continuously track products and SKUs as they move through our distribution centers.
The latest update to the system also includes enhanced vision technology. It takes only a few seconds for Acumax® to scan an image or QR code and retrieve the data held within, which enables us to transfer products through our distribution centers faster than ever before.
Delivering the right medications at the right time
The final stage of the supply chain – delivering medications and products to our customers – is often the most critical. Our customers count on us to maintain the quality of products while in transit and ensure they arrive to the right location at the right time. With our legacy of distribution, we’re able to make that happen for patients nationwide with the help of our proprietary technologies that allow us to drive 99% order accuracy.
Our ability to do so began in the 1990s with the creation of the Closed Loop DistributionSM, the industry’s first Palm-based technology that improves automated pharmacy receiving and ordering. Intended to “close the loop” between our team and the pharmacy, the solution was the first delivery system for pharmaceutical distribution.
It was developed to reduce the need for pharmacists to manually sign for orders by enabling electronic signatures and sending automatic responses. This alleviates delays and paperwork and allows them to track orders to ensure medications arrive on time.
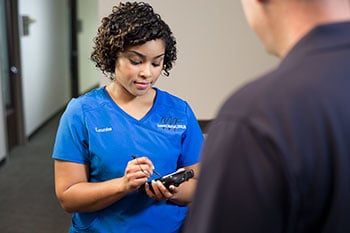
Electronic signatures via the Closed Loop DistributionSM alleviates delivery delays and allows our customers to track orders to ensure medications arrive on time.
Since then, the Closed Loop DistributionSM has upgraded to a full-scale delivery visibility system. Utilizing internet of things enabled technology, we work with IT industry partners to send and analyze data to enhance our supply chain. We’ve modernized our distribution, transportation and operations so our customers receive instant updates on daily routes and deliveries.
And we continue to be focused on ways to improve visibility into delivery times. Alongside our partners, we’re able to capture real-time data from couriers as they make deliveries. It enables couriers and pharmacists to be looped into real-time video monitoring and tracking to anticipate deliveries and plan for shipment arrivals.
Where we’re headed: advancing the future of pharmaceutical delivery
As we look ahead, we continue to embrace new technologies like artificial intelligence and machine-to-machine communication within our distribution centers to improve operational excellence.
We’ve been pioneers from the start. And while our distribution successes and stats reflect our patient-first approach, we’re always investing in new technologies to provide the best possible experience. Some of the latest advancements include automated picking and packing solutions and robotics, which help us improve productivity because we’re able to pick more accurately and pack medications faster, so they arrive to customers quicker.
Ultimately, we have a goal to bring forth cutting-edge products, solutions, and services. It’s as true today as it was nearly 200 years ago and will continue to be in the decades to come.
Share
Post
Post
Email